Ever wondered how some pumps manage to handle thick, viscous liquids or even containments with solids? Look no further than the diaphragm pump.
Unlike other pumps that use impellers or gears, diaphragm pumps rely on a unique mechanism that offers distinct advantages.
Let’s delve into the world of diaphragm pumps, exploring their working principle, key applications, and the benefits they bring to the table.
Inside the Pump: The Magic of Diaphragms
So, how does a diaphragm pump work? Imagine a pump with flexible membranes separating the fluid you want to move from compressed air. That’s the core concept of a diaphragm pump. Here’s a breakdown of how a double diaphragm pump works:
- Double Trouble: Most diaphragm pumps are double diaphragm pumps. You have two flexible diaphragms on either side of a chamber.
- Air Power: Compressed air enters a control valve, directing it to one side of the chamber.
- Diaphragm Dance: The pressurized air pushes on a diaphragm, causing it to expand. This creates a suction effect on the opposite diaphragm in the other chamber.
- In Comes the Liquid: Due to the pressure difference, liquid gets pulled into the chamber through an inlet check valve.
- The Flip Side: The control valve then switches, sending compressed air to the other chamber.
- Out it Goes: The previously expanded diaphragm gets squeezed, pushing the liquid out of the chamber through a discharge check valve. This cycle repeats continuously, creating a smooth flow of liquid.
Key Components of a Diaphragm Pump
Now that you grasp the basic principle, let’s look at the essential components:
- Diaphragms: The heart of the pump, these flexible membranes are made of various materials like elastomers or PTFE depending on the application.
- Check Valves: These one-way valves ensure the liquid flows in the desired direction, preventing backflow in diaphragm pumps.
- Air Control Valve: This valve directs compressed air to the appropriate chamber, controlling the pumping action in electric diaphragm pumps and pneumatic diaphragm pumps (also known as AODD pumps).
- Manifolds: These connect the pumping chambers to the inlet and outlet for efficient fluid flow.
Applications: Where Diaphragm Pumps Shine
Diaphragm pumps find use in various industries due to their unique capabilities:
- Chemical Processing: They handle corrosive liquids safely because the fluid never comes in contact with the pump’s working mechanism, making them ideal for chemical transfer applications.
- Food and Beverage: They can pump viscous liquids like syrups and jams without damaging them.
- Pharmaceutical Manufacturing: They ensure sterile transfer of liquids due to their self-priming ability and ability to handle shear-sensitive materials.
- Water Treatment: They efficiently move contaminated water, sludge, and abrasive materials, making them valuable tools in water treatment plants.
- Mining and Construction: They can handle abrasive slurries and grout with ease.
- Printing Industry: They precisely transfer inks and solvents without pulsation issues, ensuring consistent printing quality.
These are just a few examples. Diaphragm pumps find applications anywhere you need to move liquids that are:
- Viscous: They can handle liquids with high viscosity without compromising flow rate in positive displacement pumps.
- Shear-Sensitive: They won’t damage delicate liquids by avoiding high shearing forces.
- Contaminated: They can handle liquids with solids or abrasive materials, making them suitable for hazardous environments.
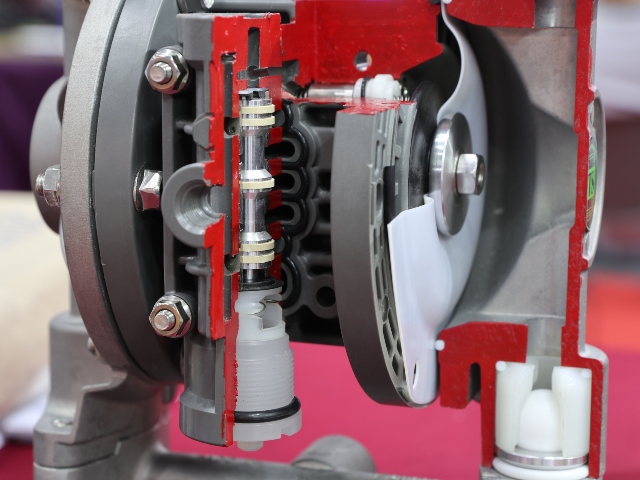
The Allure of Diaphragm Pumps: Unveiling the Benefits
So, what makes diaphragm pumps so desirable? Here are some key benefits:
- Versatility: Diaphragm pumps can pump a wide range of liquids, making them ideal for various applications.
- Self-Priming: They can start pumping even without liquid in the chamber, saving time and effort.
- Run-Dry Capability: They can operate without damage even if there’s no liquid available momentarily, unlike many other positive displacement pumps.
- Gentle Pumping: They minimize shear on delicate liquids, making them perfect for handling shear-sensitive materials.
- Durable Design: With fewer moving parts, they offer reliable operation and require minimal maintenance.
- Dry Run Capability: They can run without liquid for short periods, unlike other pumps that might seize.
Beyond the Basics: Special Types of Diaphragm Pumps
The world of diaphragm pumps isn’t limited to the standard double-diaphragm design. Here are some variations you might encounter:
- Air-Operated Diaphragm Pumps (AODD Pumps): These rely on compressed air for operation, making them ideal for remote locations or explosive environments where an electric motor might be a safety hazard.
- Electrically Operated Diaphragm Pumps: These use an electric motor to drive the pumping action, offering precise control over flow rate and making them suitable for applications requiring consistent flow.
- Linear Diaphragm Pumps: These have a single, reciprocating diaphragm for simpler applications with lower flow rates.
The Future of Diaphragm Pumps: Innovation and Advancements
Diaphragm pump technology is constantly evolving. Here’s a glimpse into what the future holds:
- Material Advancements: Development of new diaphragm materials with enhanced chemical resistance and durability, allowing for use in even harsher environments.
- Smart Pumps: Integration of sensors and control systems for real-time monitoring of factors like pressure and flow rate, enabling automated operation and predictive maintenance.
- Energy Efficiency: Focus on designing pumps with lower air consumption and improved energy efficiency, making them a more sustainable choice.
In Closing
Diaphragm pumps offer a simple and effective solution for tough jobs. Whether you’re battling gooey jams or abrasive slurries, these pumps take the mess in stride. So, next time you need a reliable partner for your liquid transfer challenges, consider the power of the diaphragm pump. You won’t be disappointed!